Fish feed production is an important factor in large-scale fish farming and aquaculture, and has a great impact on fish growth efficiency and aquaculture costs. In the past few decades, the use of floating fish feed has increased significantly because it is a high-quality environmentally friendly fish feed with superior water stability, better floating characteristics, less pollution and zero waste. All these make it an irresistible trend for the development of aquaculture feed industry.
The complete fish feed production line is composed of hammer mill, crusher, mixer, dryer, cooler and other equipment. It uses corn, corn, forage, molasses and other grains as raw materials to produce high-quality and highly nutritious fish feed.
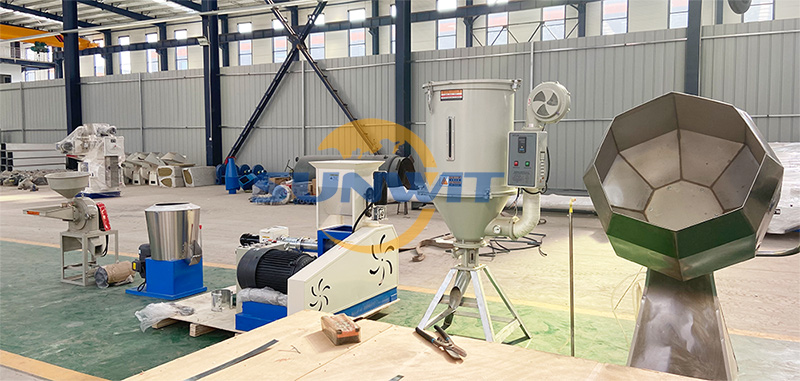
Sunwit 200kg/h Fish Feed Production Line for Sale
Floating Fish Feed Manufacturing Process
Selection of Raw Material
When selecting raw materials for fish feed processing, remember that the final product must be stable in water. The main nutrients are starch, with 10% to 15% of feed for sunken fish and over 20% of feed for floating fish. The starch content is generally between 5% and 60%. Carbohydrates act as emulsifiers, suspending agents and binders in extruding fish feed pellets.
Material Grinding
The crushing process is mainly used to grind the raw materials to the required size. Hammer mill is generally used for fish feed production of 150-700kg/h, and water drop crusher is generally used for fish feed production of 1-10 tons/h. Large-scale aquatic feed production enterprises generally adopt the secondary crushing process, that is, conventional crushing first and then fine crushing.
Material Mixing
This process is essential for the production of fish feed. The physical properties of the raw materials determine how fast you can complete this process. When adding various materials to the blender, it is best to add some large materials first, and finally add some small materials, such as a premix of minerals, vitamins, and drugs.
The mixed liquid is generally allowed to contain more than 10% of the liquid. Before adding liquid or oil, make sure that the dry ingredients in the blender are properly mixed (dry mixing). After spraying liquid or oil on top of the dry mixture, you need to mix again (wet mixing). However, some fish feeds may require moist ingredients.
Extruding Process
The design of the granulation process and the selection of related equipment are important factors affecting the quality of aquatic feed. We have dry type and wet type fish feed extruders for granulation. Wet extruders require modulators and steam boilers, while dry fish feeders do not. The former is suitable for large-scale fish feed pellet plant, the latter is more suitable for small and medium-sized feed pellet users or fish feed pellet plant. Through different parameters, the extruder can produce buoyancy, sinking, slow speed and semi-humid feed, which can adapt to the feed requirements of various aquatic animals.

Pellets Drying
Our mesh belt dryer is a continuous convection belt dryer. The pellets formed by the extruder are layered and stacked on a steel wire mesh or perforated plate belt conveyor, and are continuously conveyed through the drying chamber. In this process, the dry air repeatedly passes through the product layer until the particles reach the optimal moisture content and leave the dryer. If you choose a wet-type fish feed machine, we recommend a gas-based pellet dryer.
Pellets Spraying/Coating
In order to obtain a better sense of smell and taste, the oil sprayer can be used to spray oil onto the surface of the fish feed particles coming out of the dryer. Spray the atomized oil on the surface of the particles at high speed, and the excess oil can be recovered by filtration.
Pellets Cooling
After spraying, the fish feed pellets are transported to a counter-flow cooler for cooling. The counter-flow cooler has the advantages of small air volume, high degree of automation, small footprint, low energy consumption when processing floating fish feed particles.
Pellet Packing—electronic Packing Machine
In order to make the finished particles easy to store, transport and attract customers’ eyes, they should be packaged properly. Our electronic weighing packaging machine can automatically complete the pellets into bags, weigh, convey and seal, which greatly saves manpower and time and meets the requirements of large-scale production. This machine can be equipped with automatic hot coding, automatic bag sewing, automatic thread cutting and other functions.
Advantages of Floating Fish Feed
- High Nutrition Retention – Floating fish feed can stay on the water for a long time. When feed is dissolved in water, it loses some nutritional value. Floating fish feed can save about 20% of material loss due to water, mud and waste. High-quality fish feed floats on the water for at least 10 hours.
- Monitoring the Fish – The consumption of floating feed helps to monitor the appetite of the fish, because the fish can be seen from the shore of the wetland while eating. In addition, the health and vitality of the fish can be regularly observed.
- Environment-friendly – Floating fish feed is very easy to see. Even some remaining feed can be picked up and dried. This kind of feed can be used later, and it also helps to keep the water clean. This is very beneficial to the growth of fish and environmental protection.
- Easy to Store – Due to high temperature and pressure expansion, the water content of the floating feed (8-9%) is very low. This is why feed pellets are hard and stable. In addition, due to its low moisture content, it is easier to store.